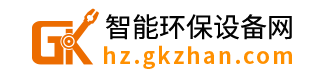
手机访问更快捷
安卓版
营销推广更便捷
一、技术原理与系统构成
1.1 正压气力输送原理
正压气力输送系统通过罗茨风机或空气压缩机产生高压气流,将粉煤灰从电除尘器灰斗输送至终端灰库。其核心在于利用管道内正压差推动物料运动,结合仓泵等发送装置实现间歇式或连续式输送。根据输送浓度,系统可分为稀相输送(气固比<15)和密相输送(气固比>50),其中密相输送因能耗低、磨损小,在电厂应用中更具优势。
1.2 系统核心组件
气源设备:罗茨风机适用于中短距离输送,空气压缩机则用于长距离、大容量场景。
发送装置:仓泵(如MD泵、AV泵)通过压缩空气将粉煤灰分批送入管道,避免管道堵塞。
输送管道:采用不锈钢或碳钢材质,直径从几百毫米到几米不等,直管段磨损较轻,弯头需特殊防磨设计。
分离与除尘设备:旋风分离器实现粗颗粒分离,袋式除尘器捕捉细颗粒粉尘,确保排放达标。
控制系统:PLC系统实时监测压力、流量等参数,实现自动化控制与故障预警。
二、运行优化与关键技术
2.1 堵管问题与解决方案
堵管是正压输送系统的常见故障,主要原因包括:
煤灰含水或异物:通过灰斗加热除湿、控制锅炉吹灰方式降低含水率。
管线布置不合理:减少弯头数量,控制输送高度差(一般不超过20米)。
临界流速失衡:根据公式Vt=Kds(0.1744/μρ0)(1/3)(gρs)(2/3)调整气流速度,确保物料悬浮。
双套管紊流技术:在输送管内设置内管,通过开口设计实现气流扰动,自动疏通堵塞。
2.2 磨损问题与防磨措施
刮削磨损:与管道内壁粗糙度相关,需降低流速或增加耐磨涂层。
压削磨损:多发生于弯头,需采用梯形衬板防磨弯头或矩形截面防磨弯头,延长使用寿命。
材料选择:直管段可采用普通碳钢,弯头需内衬陶瓷或喷涂耐磨涂料。
2.3 热控问题与解决方案
粉煤灰输送过程中因摩擦生热,可能导致管道温度升高,影响输送效率。解决方案包括:
管道保温:减少热量散失,降低能耗。
冷却装置:在高温区域增设冷却水套或风冷系统。
热平衡分析:通过仿真模拟优化气流参数,避免局部过热。
三、典型应用案例
3.1 大型燃煤发电机组应用
某600MW机组采用正压浓相气力除灰系统,设计为一级输送,通过MD泵将电除尘器灰斗的粉煤灰直接输送至灰库。系统运行初期出现堵管问题,通过以下措施优化:
在输灰一电场入口增设旁路,增大气源流量。
在水平段补气,推动料栓前移。
增设事故放灰管与气化风装置,缓解落灰问题。
优化后,系统输送效率提升30%,排堵阀更换频率降低80%。
3.2 陡河发电厂干除灰系统
陡河发电厂采用英国克莱德厂家设计的干除灰系统,因煤质变化频繁导致堵管频发。通过以下改进实现稳定运行:
加强参数调整,结合煤质变化实时优化输送压力与流速。
在输灰管道沿线增设辅助输送气,增强介质流动性。
采用双套管紊流技术,降低堵塞风险。
四、技术优势与应用价值
4.1 技术优势
高效输送:密相输送速度低(3-10 m/s),能耗较稀相输送降低40%以上。
环保节能:全密闭输送避免粉尘泄漏,符合超低排放要求。
灵活布局:管道可垂直、水平或倾斜布置,适应复杂地形。
自动化控制:PLC系统实现无人值守,降低人力成本。
4.2 应用价值
生产连续性保障:确保粉煤灰及时转移,避免影响锅炉运行。
资源再利用:集中输送的粉煤灰可用于建材生产,创造经济价值。
环保效益:减少厂区扬尘,降低环境污染风险。
五、未来发展趋势
5.1 智能化升级
结合物联网与大数据技术,实现输送系统的远程监控与自适应调节。
5.2 节能降耗
开发高效低能耗气源设备,优化管道设计以减少压力损失。
5.3 多功能集成
在输送过程中集成干燥、冷却等工艺,提升系统综合效益。